Плазменная резка представляет собой процесс, в котором используется высокоскоростная струя ионизированного газа. Эта струя, нагретая до состояния плазмы, проводит электричество от плазменного резака к заготовке. Тепло расплавляет материал, в то время как высокоскоростной газ выталкивает расплавленный металл, создавая разрез.
Основы плазменной резки
Процесс начинается с зажигания высокочастотной электрической дуги внутри резака. Затем сжатый газ, обычно воздух или смесь газов, направляется через небольшое отверстие. Когда электричество от резака проходит через этот газ, он нагревается до состояния плазмы, способного резать электропроводящие материалы с высокой скоростью и точностью. Например, типичный ручной резак может резать сталь толщиной до 38 мм со скоростью примерно 20 дюймов в минуту, в зависимости от выходной мощности резака, которая обычно составляет от 12 до 60 ампер.
Достижения в технологии
Недавние технологические усовершенствования повысили эффективность, качество и удобство процесса. Например, инверторная технология уменьшила размер и энергопотребление устройств, одновременно увеличив скорость резки и улучшив стабильность дуги.
Современные инверторы могут увеличить выходную мощность до 80% эффективности, что со временем приведет к значительной экономии средств. Более того, производители интегрировали технологию ЧПУ в аппарат плазменной резки, что позволяет выполнять точную автоматическую резку по сложным шаблонам. Эти приборы с ЧПУ могут достигать точности резки 0,01 дюйма, что жизненно важно для высокоточных приложений.
Многие системы теперь оснащены расширенными возможностями диагностики, что значительно упрощает устранение неисправностей и техническое обслуживание. Например, более новые модели могут сообщать о среднем сроке службы расходных материалов, таких как электроды и сопла, около 500 запусков и предоставлять пользователям подробный анализ затрат на резку на основе их конкретных моделей использования, помогая им оптимизировать эксплуатационные бюджеты.
С точки зрения безопасности и простоты использования конструкции резаков стали более эргономичными, а функции безопасности, такие как механизмы снижения напряжения, защищают пользователей во время работы. Некоторые резаки могут определять окончание срока службы расходных компонентов и вовремя предупреждать пользователей, тем самым сохраняя как качество резки, так и долговечность устройства.
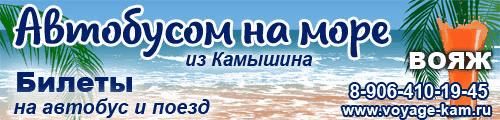